About Vacuum
Definition of Vacuum
A vacuum is a space in which almost nothing exists, including air and other gas. The pressure in a vacuum is significantly lower than atmospheric pressure. A perfect vacuum would contain no pressure at all.
How Our Vacuum Cups Work
Because Wood’s Powr-Grip® vacuum cups create a low-pressure vacuum, the high pressure of the Earth’s atmosphere pushes down on the cup with incredible force, creating a solid, temporary connection. Unlike suction cups that create vacuum as they pull away, Powr-Grip vacuum cups use a pump to remove the air from under the pad—creating a much more reliable hold. Using a pump also connects the full face of the pad to materials, minimizing risk of damage to surfaces.
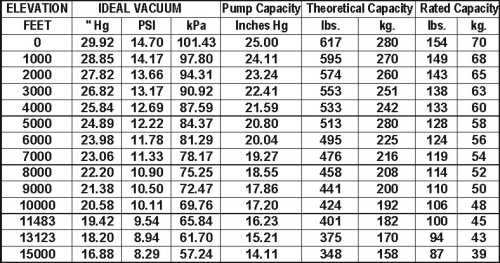
How Elevation Affects Vacuum and Vacuum Handling Devices
WPG lifters measure vacuum as the difference between pressure of the vacuum and atmosphere. As elevation increases, atmospheric pressure decreases. So the higher the elevation, the less measured vacuum a pump can produce, reducing capacity.
Determining Vacuum Lifter Capacity
This formula is used to calculate the theoretical capacity of a vacuum pad:
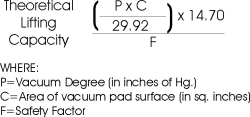
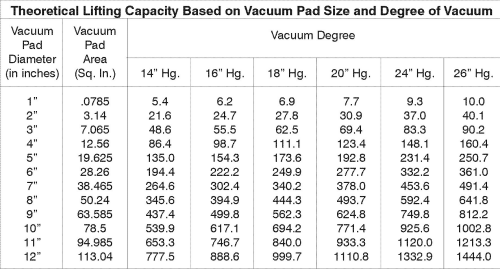
Capacities given in pounds (lbs).
You can see the results of this formula in the chart to the right:
These results are only theoretical because many factors can reduce a pad’s ability to lift a load, including: pad size and model, type of load material, load shape, vacuum pump type, and dirt/particles on the load. Safety considerations and ANSI standards also affect the determined capacity.
These formulas and charts provide theoretical lifting capacities only. Contact us when calculating capacities for any vacuum handling application.